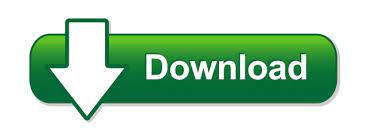

With this we were able to quickly test a variety of geometric configurations, while giving us the assurance that both the vehicle performance and stability were meeting our targets. To support this, we developed tools to estimate the open-loop dynamic modes from stability derivatives, which were calculated using MIT’s open source AVL fixed wing analysis tool. This provides some level of assurance that the vehicle dynamics will be well behaved and easy to control, which is especially important when considering management of failure modes. One of our initial design targets was to have Level 1 and Level 2 open-loop dynamic modes in the cruise configuration. The following pictures show canard, wing and winglet airfoil sections: For example, following our testing of several designs, we settled on a relatively thick airfoil that allows for efficient spar structure and internal volume for routing wires and mounting systems.
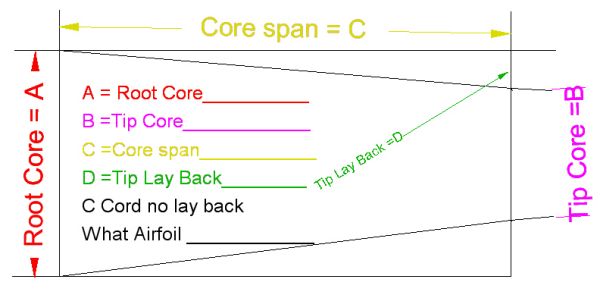
When choosing the wing, canard, and winglet airfoils, we focused on balancing competing requirements. The following figure shows the optimal load distributions for our lifting surfaces to minimize drag.įigure 3: Optimal Trefftz plane loading with e = 1.35 We settled on the non-planar tandem configuration with winglets to both lower the induced drag and reduce the interactions between the canard and wing mounted fans. In keeping with our small footprint goal, we chose to utilize a smaller wingspan (even though we knew this would lead to higher induced drag). With this in mind, we began looking at non-planar wing designs. disk loading for different VTOL vehicle types, including Vahana. After a great deal of analysis we were able to gauge performance specs that ended up being similar to tilt rotors or heavy helicopters, such as the UH-60 Blackhawk, when it comes to hover disk loading and power loading.įigure 2: Power loading vs. The red point indicates the chosen fan radius to balance vehicle size with power requirements.įigure 1: Shaft Power and FOM as a function of blade radius.Īs a reminder, some of our original key vehicle design parameters include fan diameter, total disk area, mass, fuselage length, wing airfoil, wing tilt range, etc. The figure of merit is a hover efficiency measure that is equal to the ideal hover power required from momentum theory divided by the actual hover power required. The following figure shows an example trade off between fan radius and both the hover power required and the hover figure of merit, while holding total thrust fixed. In the end, we needed to select a blade radius that would keep the footprint of the vehicle small, while ensuring the aircraft has the power required to carry its own weight (motors, fans, wings, etc.). We used a multi-disciplinary design approach that tied together aerodynamic performance estimates with an open-loop dynamics model and structural weight estimates. The first aspect to tackle was the aerodynamic surfaces on the vehicle - fans, wings, winglets, and landing gear. Here we’ll take a look back at our aerodynamic design process so you can join us in our journey.įollowing our vehicle sizing process, which we outlined in our first design-related blog post, we dove deep into aerodynamic and structural design and validation.

Since we first sketched Vahana on a napkin, we’ve eagerly looked forward to the day we would see our vision become a reality as occurred just a few weeks ago with our first successful full-scale test flights.
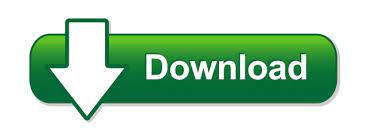